Product Information
High Speed Dispenser CPD-G2
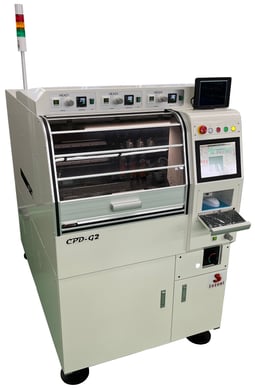
Feature
EnableFurther Small Components by Jet Dispense Head
Achieves Top Class Dispensing Tact Time
Continues High Precision Dispensing by Reliable Structure
Meets Wider Dispensing Needs with Variety Options
SPECIFICATIONS
PCB Size | 50×50~460×360mm (D-model) 50×50~510×460mm (L-model) |
Dispense Method | Piezo Type Jet, Air Pulse |
Dispense Head | 1~3 Head(s) |
Dot(s)/shot | 1 dot/shot (Jet Head), 1~4 dot(s)/shot (Air Head) |
Dispense Speed (at Optimum Condition) |
0.05sec/shot (Jet Head) 0.07sec/shot (Air Head) |
Accuracy | ±50μm |
Rotation | ±90°, (±180°: Option) |
Nozzle | 1~4 dot(s), Center Stopper, Non-Contact, etc. |
Syringe | 30cc (10cc, 20c : Using Adapter) |
Conveyor | Automatic Width Adjustment |
OS | Windows10 |
Operation | Touch Panel |
Air Supply | 0.5MPa Clean and Dry Air (40Nl/min) |
Power Supply | Single phase 200, 220V, 3.0kVA |
Size
Lead-Free N2 Reflow Oven SRF8225NⅡ
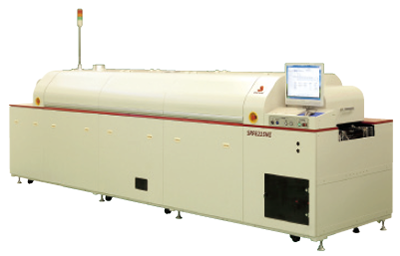
Feature
Low Nitrogen Consumption
Powerful Heating / Cooling Capability
New System for Countermeasure against Flux
SPECIFICATIONS
Dimensions | 4,446(L)×1,090(W)×1,350(H)mm (Excluding Projection) |
Conveyor Height | 900±30mm |
PCB Size | 40×50~250×330mm Mounted component height: ±25mm |
Zone | Heating: 8 zones Cooling: 2 zones |
PCB Holding | 3mm from PCB edge |
Controller | PLC (Main) PC (Display, Operation, and Profiler) |
Utilities | Air Supply : 0.5MPa Clean and Dry Air N2 Gas Supply: 0.5MPa (max: 150 /min.) |
Power Supply | 3 phases 200V±10V 50/60Hz 35kVA |
Weight | Approx. 1,500kg |
Zone Configuration
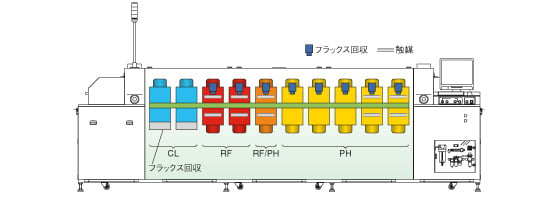
Size
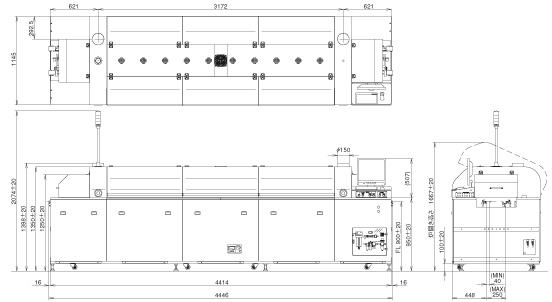
LED flip-chip mounting device BDM-1000

Features
Flip-chip mounting through innovative direct wafer
Next generation rapid productivity which far outperforms existing bonders
First ACP batch wafer transfer system in the world
Mini LED compatible
Self-alignment control through optimization of ACP membran